The art of glass, with its corollary of traditions and characteristics, has always linked its name to that of Venice and Murano.
A very ancient art that has been able to transform incandescent and amorphous masses into masterpieces, and that has withstood the passage of centuries and epochs, arriving to the present day more alive than ever.
We will discuss about history and characteristics of this noble art, but if you are still curious, you could enjoy the visit to the interesting Glass Museum, about which we talk at the end of the article.
Let our glassy journey begin!
The origins of glass: a discovery by accident
The very first evidence of the presence of glass working in Venice dates back as far as 982 by a bottle maker, a certain Dominicus Phiolarius.
But what are the origins of glass? The "discovery" seems to be attributed even to the Phoenicians. It seems they have been the first to carry out a primitive processing and, as often happens, the discovery was born in a completely fortuitous way.
It was only a question of a fire lit for a long time on the sand. The high temperature melted the grains turning them into a sort of honey, which once solidified took on the appearance of a glassy mixture. That was it!
The processing of glass, at first very basic, then spread to the Roman Empire, where they used it mainly for a purely domestic and religious use.
The history of glass, from East to Venice
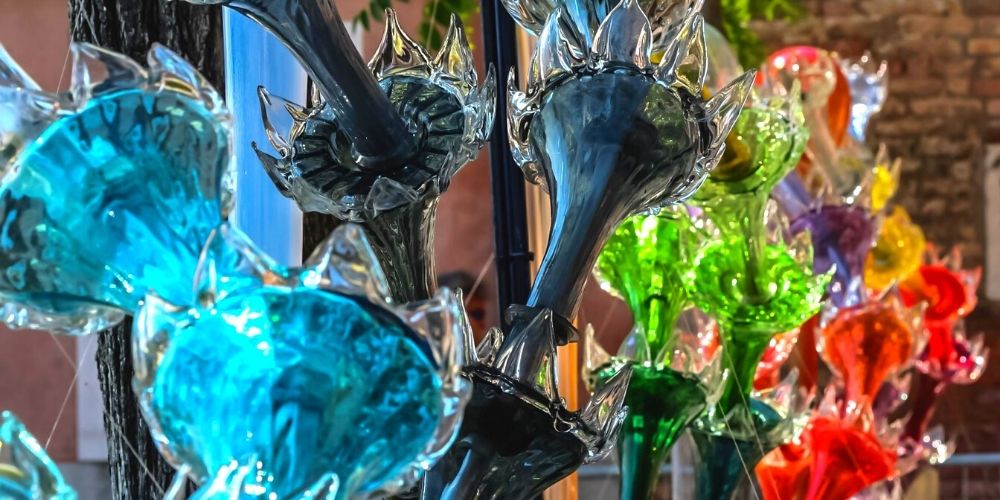
It was the Romans the first to introduce the glass to Venice. Later, the people who came from the East, thanks to the intense trading that the Serenissima had shared with the East.
Then, the inhabitants of Constantinople brought to the city their vast knowledge of working techniques.
The witty spirit and farsighted views of the Venetians then did the rest. They immediately understood that before the incandescent mass cooled, it was possible to mold it and enrich it with bright colors that remained unchanged until the object was completed.
Thus was born the extraordinary art of Murano glass, with its incredible technical and aesthetic characteristics.
But the most important thing that the Republic of Venice understood had to do with a long-term, revolutionary project, we could say.
The industrial revolution in Murano
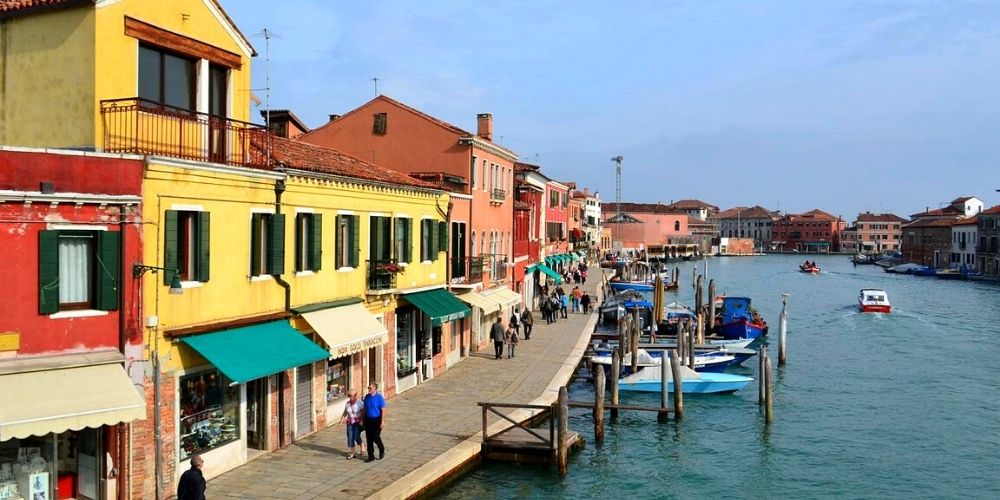
Glassmaking could become an important driving force for the state's commercial development. Thus it was that great effort was put into perfecting the workmanship and protecting this art, but also into promoting it.
Before long, a series of laws were enacted that favored the domestic development of glassmaking, categorically prohibiting the import of the foreign product. The same prohibition also affected individual artisans: it was forbidden for foreign glassmakers to work in the Lagoon.
At first, the furnaces were concentrated in Rivo Alto, today's Rialto area, later expanding to the Sestiere of Dorsoduro. In those areas, kilns were lit daily and true masterpieces were made.
Everything changed in the 13th century, when Doge Pietro Gradenigo decreed that all the furnaces be moved to the island of Murano.
The moving of the furnaces from Venice to Burano
.jpg)
Why were the furnaces moved to a small island in the Venetian lagoon?
The main reason, we might say official, was related to the intention to avert fires in the city because of the frequent fires that developed from the furnaces. They threatened to burn down most of the dwellings, which were mostly made of wood.
There was, however, a second, we might say unofficial, motivation. The Republic's intention was to isolate workmanship and workers from all those prying eyes that daily crowded the Serenissima. Therefore, a detached and isolated place, completely outside the city dynamics, was preferred.
It was necessary to guard and protect the secrets of an art, and Murano was the most suitable place. So it was that the Venetian Republic unknowingly initiated a kind of industrial revolution, a full five centuries before the more famous one.
Moving the furnaces to Murano, however, involved relocating the master glassmakers and their families, and certainly not everyone agreed.
On the other hand, who would have preferred a quiet island in the Northern Lagoon to a thriving and wealthy city?
The privileged class of master glassmakers
The impetus to accept the change came from the Republic itself, which offered a series of incentives to individual artisans and their families.
The master glassmakers were thus able to achieve a high social status by becoming a protected and privileged Corporation as never before. As proof of this, a statute of rights and duties, was issued in 1441.
They were allowed to carry a sword, marry members of the nobility, and even be immune from prosecution. These benefits were also enjoyed by their family members, as already mentioned, and especially their children.
Magnanimity on the part of the Republic? Not really. It was merely a ploy to encourage new recruits to learn the trade, so that it could be handed down from father to son in an endless passage.
The duties of master glassmakers
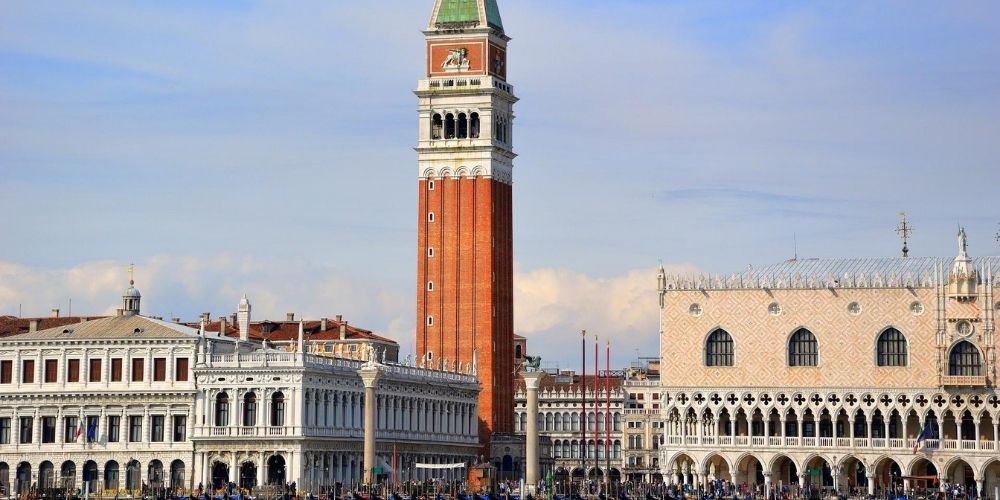
As it often happens, however, when the Republic gave, it then also found a way to take away.
And so the benefits were also accompanied by a series of limitations and restrictions, which in some cases were really harsh.
Master glassmakers were a protected category, certainly, but they were also well guarded. As a matter of fact they were absolutely forbidden to leave the territory of the Republic except with a permit requested and issued by the customs authority. Those who dared to leave the city without prior permission were disbarred for life from the guild without the possibility of ever being able to practice their profession again.
But there was even worse! Sharing abroad features and techniques of Murano glass was punishable by death penalty, carried out three the columns of St. Mark's.
In fact, in 1675 one of Murano's best craftsmen, Gerolamo Barbarin, reached Versailles and worked on the palace's famous Hall of Mirrors. Without batting an eye the Serenissima condemned him to death. But his exceptional skill pardoned him and he was allowed to return home.
Even in that case, however, the state thought of itself, and of the professional potential of the individual craftsman, certainly not of saving a man's life.
Such episodes, however, did not happen again anyway.
How is glass made? Methods and charaterstics
Even today, glassmaking follows old-fashioned techniques and methods.
The main component is silica sand, which must be very pure. Then soda ash is added, with the task of lowering the melting temperature. Finally the lime, sodium nitrate and potassium carbonate.
These elements once arrived in a furnace are mixed together and melted in a rather complex process at a temperature of up to 1400 Celsius degrees. An extremely malleable glowing mass is obtained.
At this point, the master glazier inserts a long metal rod inside the furnace, spinning it continuously so as to draw out the necessary amount of product. Once it has been extracted, with rather simple tools, the creative phase begins, which then leads to the finished product.
In the days of the Serenissima Republic, this processing led to the production of mainly bottles and mirrors, in which the Venetians were absolute experts, holding the reins of this trade throughout Europe.
After the furnaces were relocated to the island of Murano, the proximity of all the master craftsmen led to an exchange of knowledge that was fundamental to making significant innovations.
Muran glass through the ages
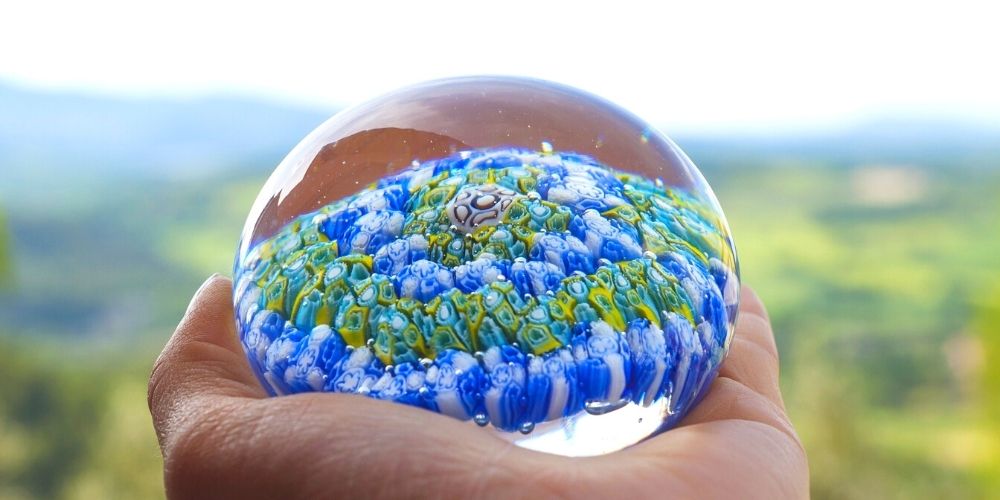
It was in the 15th century when master Angelo Barovier devised the formula for making completely transparent glass. This made it possible to make glasses and pitchers, but above all the world's first pure and truly reflective mirrors.
After two centuries, master Giuseppe Biati made the first flowered chandelier. This was a workmanship in great demand by all noble families to embellish the halls of their palaces. Among the most beautiful and largest was the one in the Salone da Ballo di Cà Rezzonico and the one in the stalls of the Gran Teatro La Fenice.
Between the 15th and 18th centuries, however, Murano pearls were made. These small and colorful glass spheres that were extraordinarily successful, even becoming a bargaining chip to obtain products such as spices, ivory and even slaves. They were renamed, in fact, trade pearls or slave pearls.
Legend also has it that Christopher Columbus, who arrived in the Americas in 1492, brought a bag full of pearls as a gift to the people of San Salvador.
In time, the workmanship was perfected with the microscopic Rocailles beads. They were made by creating glass rods, long straight filaments with a really small diameter. The master glassmakers would blow inside to create an air bubble that would later become the pearl hole.
They were used for the decoration of dresses and bodices, embroidery and even jewelry production, attracting the attention of noblewomen in courts throughout Europe.
It was the end of the 19th century when master Vincenzo Moretti made the first murrina instead, being inspired by ancient Roman mosaics. It is a workmanship that allows elements of many vibrant colors to be trapped in a transparent mass. Complex but extremely fascinating.
From the end of the Serenissima to modern design
Venice and Murano remained absolute powers for glass working for centuries, surviving quite discreetly even after the fall of the Republic by Napoleon in 1797.
The real crisis for Murano glass came with Austrian domination. Austria, in fact, was the home of Bohemian crystal, a particular decorated glass obtained by mixing sodium chloride and gypsum, leading to a final product that was completely colorless and above all more stable than that of Murano.
It is easy to imagine that the Austrians promoted their local glass despite that of Laguna. In their 20 years of domination they drastically reduced the import of Venetian products and substantially taxed the raw materials necessary for processing.
So it was that more than half of the furnaces in Murano extinguished their fires, forced to close under the weight of a great financial crisis. The few that remained open only produced bottles and pearls, absolutely not enough to keep the engine of the entire island's economy running.
It would be necessary to wait until the end of the nineteenth century for the art of Murano glass to be relaunched. The fires of the furnaces were rekindled by two enterprises, that of the Toso Brothers and that of Salviati family: within 10 years they brought Murano glass back to its ancient splendor, becoming a real flywheel for the new commercialization in Europe and the reopening of the other furnaces.
A great help to the revival of glass was given by the Venice Biennale which, in its first kermesse dedicated to art, hosted many master glassmakers and their works, opening the way to an exquisitely modern design. It was 1895 and since then the art of Murano glass has continued to shine, taking back the world record of its kind, then knowing how to renew itself and adapt to fashions and times.
A milestone in this direction was the Venini that from 1921 gave life to an exclusively modern design production that also saw the collaboration of the great names in contemporary art.
The characteristics of the glass blowing art today
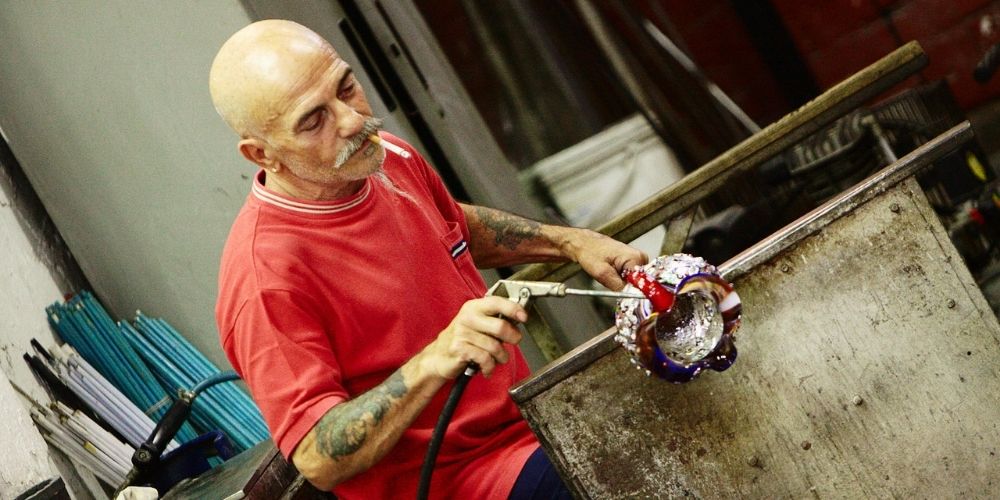
Today the island of Murano has about 80 furnaces, preferring three types of processing.
- The most famous mouth-blown glass, made by inserting air with the blow pipe into the incandescent mass that swells like a balloon: the master glassmaker's ability to give the desired shape in a rather short period of time, before the cooling and solidification of the mass, is fundamental. The main characteristic of this type of glass is the thinness and lightness given by the balance between solids and voids.
- The solid glass, used for the creation of real glass sculptures: a primary central body to which other glass grafts are then progressively added, to create simple faunal figures or human bodies of colossal dimensions and in various attitudes.
- Finally, the working of mirrors decorated in the most varied ways, to enrich walls or to be inserted in wooden furniture. To these are added glasses and pitchers, chandeliers, and the small workmanship of pearls, murrine and jewelry.
Around Venice and Murano, there are many Muran glass sellers, even too many, because they are not all original.
Real Murano glass must bear the words Made in Murano, otherwise it is almost certain that it is not really authentic.
To learn more, you might visit the Glass Museum. Located right on the island of Murano, the museum traces the mystery of the history and characteristics of glass, showing its visitors exhibits from the glorious past.
Enriching the guided tour is a collection of unique pieces produced from the 14th century to the present day.
And there's more! The Glass Museum is one of the attractions included in the Venice Pass!
Visit the website to learn more and... Beware of imitations!
Lascia un commento